Machined Casting: A Comprehensive Guide to the Process, Benefits, and Applications
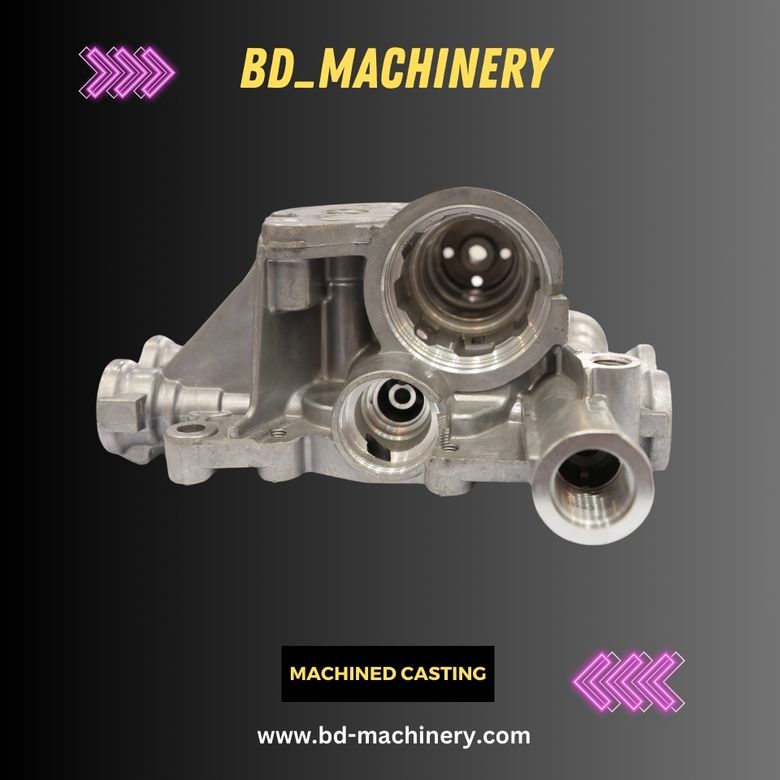
Machined casting combines the advantages of casting, which allows for complex shapes and cost-effective production, with the precision and accuracy of machining. In this comprehensive guide, we will delve into the process of machined casting, explore its benefits over traditional casting methods, and discuss its wide-ranging applications across industries.
Section 1: Understanding Machined Casting
1.1 What is Machined Casting?
Machined casting refers to the process of casting a component with intricate or critical features and subsequently machining it to achieve the required dimensions, surface finish, and tolerances. It involves the integration of casting and machining techniques to produce high-quality, finished parts.
1.2 The Machined Casting Process:
The machined casting process typically involves the following steps:
- Pattern Creation: Develop a pattern or tooling that represents the desired shape of the final component.
- Mold Creation: Use the pattern to create a mold, typically made of sand or other suitable materials.
- Casting: Pour molten metal into the mold and allow it to solidify, forming the rough shape of the component.
- Cooling and Solidification: Allow the casting to cool and solidify fully before further processing.
- Machining: Employ various machining operations such as milling, turning, drilling, and grinding to achieve the desired dimensions, surface finish, and tight tolerances.
- Finishing: Perform additional processes like deburring, polishing, and coating to enhance the aesthetics and functionality of the machined casting.
Section 2: Benefits of Machined Casting
2.1 Complex Geometries:
Machined casting enables the production of intricate and complex shapes that may be challenging or costly to achieve through conventional machining processes alone.
2.2 Cost-Effectiveness:
By utilizing casting for the initial shape formation, machined casting reduces material waste, minimizes machining time, and lowers overall production costs compared to fully machined components.
2.3 Material Flexibility:
Machined casting allows the use of a wide range of materials, including ferrous and non-ferrous alloys, providing flexibility in material selection to suit specific requirements.
2.4 Improved Strength and Integrity:
Casting provides excellent material properties, such as improved structural integrity and reduced porosity, resulting in components with enhanced strength and durability.
2.5 Design Freedom:
The combination of casting and machining allows designers greater freedom in creating innovative and intricate designs, enabling the production of unique and customized parts.
Section 3: Applications of Machined Casting
3.1 Automotive Industry:
Machined casting finds extensive use in the automotive sector for manufacturing engine components, transmission parts, suspension components, and brake system parts.
3.2 Aerospace and Defense:
The aerospace and defense industries rely on machined casting for producing critical components such as turbine blades, structural components, and complex aerospace parts.
3.3 Industrial Machinery:
Machined castings are widely used in the manufacturing of machinery components, including gears, valves, pumps, and hydraulic systems.
3.4 Energy Sector:
Components used in power generation equipment, such as turbines, generators, and heat exchangers, often benefit from the machined casting process due to its ability to produce intricate shapes with high accuracy.
3.5 Medical Equipment:
Machined casting plays a vital role in the production of medical equipment components, including prosthetics, orthopedic implants, and surgical instruments.
Conclusion:
Machined casting offers a versatile and cost-effective solution for manufacturing complex components with high precision and quality. By combining casting and machining techniques, this process enables the production of intricate shapes while maintaining tight tolerances and surface finish requirements. Understanding the machined casting process, its benefits, and various applications across industries will help manufacturers make informed decisions and leverage this advanced manufacturing technique to its fullest potential.