What Makes Abrasive Waterjet Cutting a Game-Changer for Precision Manufacturing?
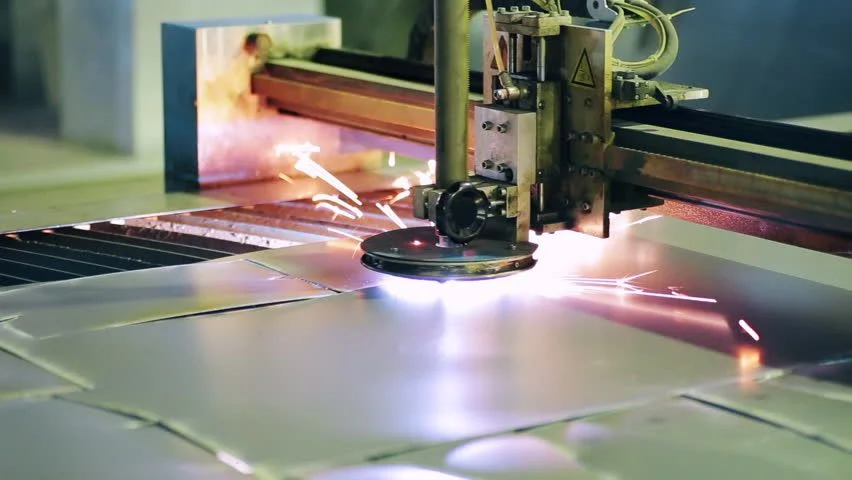
How Abrasive Waterjet Cutting Machines Are Revolutionizing Precision ManufacturingIntroduction
In the ever-evolving landscape of precision manufacturing, technology has played a crucial role in pushing the boundaries of what is possible. Among the most groundbreaking innovations in recent years is the rise of abrasive waterjet cutting machines.
These powerful tools have transformed how industries approach cutting and shaping materials, offering unmatched accuracy, versatility, and environmental benefits. This article explores how abrasive waterjet cutting machines are revolutionizing precision manufacturing, their unique advantages, and the future they hold for the industry.
What Are Abrasive Waterjet Cutting Machines?
Abrasive waterjet cutting machines use a high-pressure stream of water mixed with abrasive particles (such as garnet) to cut through hard materials. Unlike traditional cutting methods that rely on heat or mechanical force, waterjets harness the power of accelerated erosion. This process allows for extremely precise cuts without compromising the material’s structural integrity.
The machine works by pushing water through a small nozzle at pressures up to 90,000 psi. When mixed with abrasive particles, the water stream becomes powerful enough to slice through metals, composites, ceramics, glass, and even stone. The result is a clean, smooth cut with minimal waste.
According to a Abrasive Waterjet Cutting Machines Market report, the industry is expected to grow significantly in the coming years.
Key Advantages of Abrasive Waterjet Cutting Machines
- Unmatched Precision and Accuracy Abrasive waterjets can achieve cutting tolerances as tight as 0.001 inches. This level of precision makes them ideal for industries where accuracy is paramount, such as aerospace, medical devices, and electronics manufacturing. The non-thermal cutting process ensures no heat distortion, keeping even the most delicate materials intact.
- Versatility Across Materials One of the most impressive aspects of waterjet technology is its versatility. It can cut virtually any material, including:
- Metals (steel, aluminum, titanium)
- Composites (carbon fiber, fiberglass)
- Glass and ceramics
- Plastics and rubber
- Stone and concrete This wide range of compatibility eliminates the need for multiple cutting tools, streamlining production lines and reducing costs.
- Environmentally Friendly Unlike laser or plasma cutting, abrasive waterjets do not produce hazardous fumes, dust, or heat-affected zones. The process uses minimal water, which can be recycled, and the abrasives are often natural substances like garnet. This eco-friendly approach reduces waste and aligns with modern sustainability goals.
- Minimal Material Waste Precision cutting means less waste. Traditional cutting methods often result in larger kerf widths (the width of material removed by the cut), but waterjets produce narrow kerfs, optimizing material usage. This reduces costs and supports lean manufacturing principles.
- Enhanced Safety Waterjet machines operate without heat, so there is no risk of burns, fires, or toxic gas emissions. Additionally, the absence of mechanical force reduces the likelihood of tool breakage or flying debris, making waterjet cutting one of the safest industrial cutting methods available.
Applications of Abrasive Waterjet Cutting Machines
- Aerospace Industry Precision is non-negotiable in aerospace manufacturing. Waterjets cut complex components like turbine blades, wing sections, and heat-resistant alloys with exceptional accuracy. Their ability to handle tough materials without compromising their integrity is a game-changer.
- Automotive Sector The automotive industry uses waterjets to cut intricate parts, including gaskets, interior panels, and custom metal pieces. The flexibility of the technology supports rapid prototyping, helping automakers innovate faster.
- Medical Device Manufacturing Medical tools and implants require micron-level precision. Waterjet cutting allows for intricate designs without introducing heat-affected zones that could compromise a device’s functionality or biocompatibility.
- Electronics Industry Delicate components like circuit boards, semiconductors, and display screens benefit from waterjet cutting’s gentle yet precise approach. The non-thermal process prevents damage to sensitive electronics.
- Architecture and Art Beyond industrial use, waterjets have found a place in art and architecture. Designers use them to create custom tiles, glass panels, and decorative stonework, achieving complex patterns that traditional tools cannot replicate.
The Future of Abrasive Waterjet Cutting Machines
As technology advances, waterjet cutting machines are becoming smarter and more efficient. Innovations on the horizon include:
- Automation and AI Integration: AI-powered software can optimize cutting paths, reduce errors, and enhance productivity.
- Higher Pressure Systems: New machines capable of exceeding 100,000 psi will enable even faster, more precise cuts.
- Enhanced Abrasive Recycling: Improved recycling systems will make the process even more sustainable.
- Compact Designs: Smaller, portable waterjets will open new opportunities for on-site industrial and artistic applications.
Conclusion
Abrasive waterjet cutting machines have undeniably revolutionized precision manufacturing. Their ability to cut a wide range of materials with exceptional accuracy, while remaining eco-friendly and safe, has positioned them as a cornerstone technology in industries from aerospace to art. As innovation drives these machines to new heights, their impact on manufacturing efficiency, cost savings, and design possibilities will only grow.
For manufacturers seeking cutting-edge solutions to stay ahead of the curve, investing in abrasive waterjet technology is more than a choice — it’s a strategic move towards the future of precision engineering.