Choosing the Right Palletizing Equipment: What You Need to Know
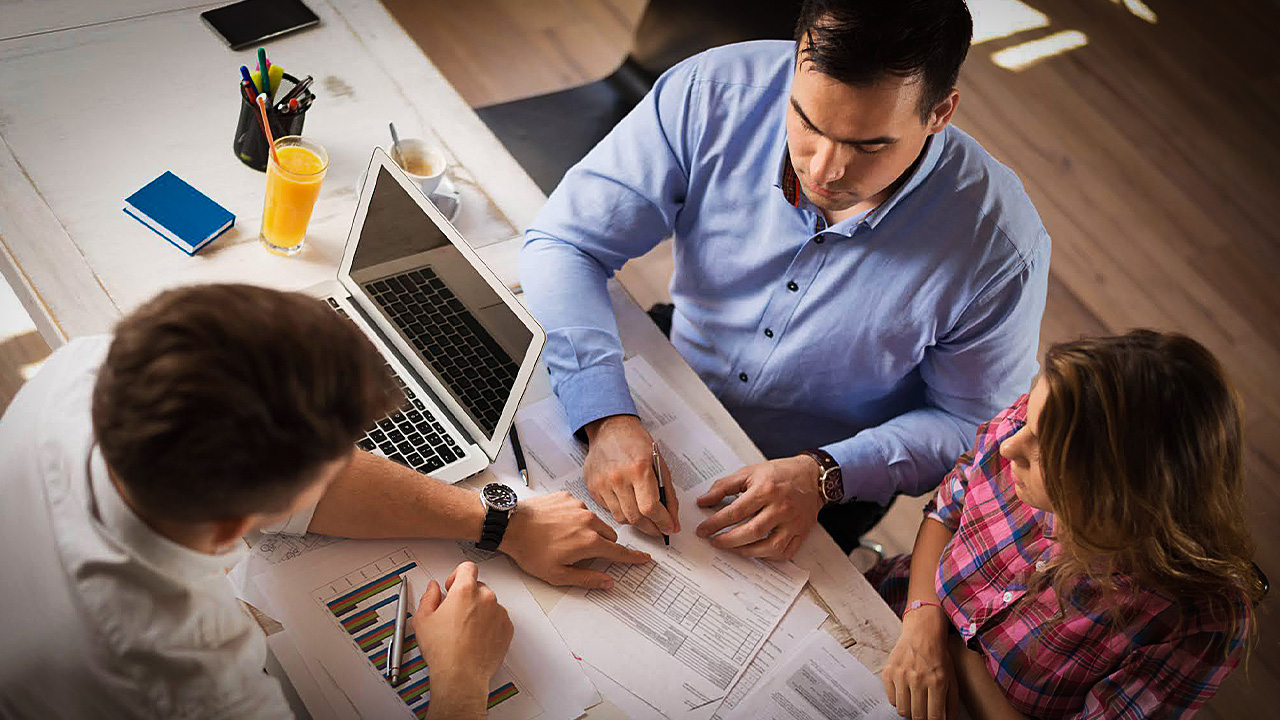
Introduction to palletizing equipment;
Palletizing equipment plays a crucial role in the efficiency of any warehouse or manufacturing operation. As products roll off the assembly line, the need to stack them securely for storage or shipping becomes paramount. With various options available on the market, choosing the right palletizing equipment can feel overwhelming. Yet, this decision significantly impacts productivity, labour costs, and even safety.
In today’s fast-paced environment, selecting suitable palletizing solutions is not just a matter of convenience; it’s essential for streamlining operations and ensuring that goods reach their destination intact. Whether you’re managing a small facility or overseeing large-scale production, understanding your options will help you make informed decisions that bolster your business growth. Let’s dive into what you need to know about choosing the ideal palletizing equipment tailored specifically to your needs!
Importance of choosing the right palletizing equipment;
Selecting the right palletizing equipment is a critical decision that can significantly impact your operations. It’s not just about getting products stacked; it involves efficiency, safety, and cost-effectiveness. The right equipment streamlines processes. This means fewer labour hours and reduced chances of errors during packing. A well-chosen system enhances throughput and ensures timely delivery to customers.
Moreover, compatible machinery adapts to specific product types and sizes. Whether you handle boxes, bags, or even irregular shapes, finding the perfect fit matters immensely. Investing in suitable palletizing solutions also promotes workplace safety. It minimizes manual handling risks for employees while promoting ergonomics in daily operations.
Lastly, consider long-term growth potential when selecting equipment. The ideal choice should be able to scale alongside your business needs without major overhauls down the line.
Different types of palletizing equipment (manual, semi-automatic, and automatic);
Palletizing equipment comes in various forms, each tailored to specific operational needs. When it comes to palletizing equipment, there are three main types to consider: manual, semi-automatic, and automatic. Each type offers its own set of advantages and choosing the right one for your needs will depend on factors such as production volume, budget, and product specifications.
1. Manual Palletizing Equipment:
As the name suggests, manual palletizing equipment requires human labour to load and unload products onto pallets. This is usually done by hand using tools such as a pallet jack or forklift. Manual palletizing equipment is ideal for small-scale operations with relatively low production volumes. It is also a cost-effective option for businesses with limited budgets as it does not require any additional machinery or automation.
However, manual palletizing can be physically demanding and time-consuming. It also poses a higher risk of worker injuries due to repetitive movements and heavy lifting. Therefore, this type of equipment is best suited for lightweight products that can be easily handled by workers without putting strain on their bodies.
2. Semi-Automatic Palletizing Equipment:
Semi-automatic palletizers bridge the gap between manual and fully automatic systems. They require some level of human involvement but also utilize machinery to assist in the loading and unloading process. This type of equipment typically uses conveyors or robotic arms to move products onto the pallets.
Semi-automatic palletizers offer increased efficiency compared to manual systems while still being relatively affordable. They are suitable for medium-sized operations that require faster production speeds but may not have the budget for a fully automated system.
3. Automatic Palletizing Equipment:
Fully automatic palletizers are the most advanced type of equipment available in the market today. These systems use computer-controlled technology to handle all aspects of the packaging process without any human intervention required.
Automatic palletizers offer high-speed operation with minimal errors and maximum precision, making them ideal for large-scale operations with high production volumes. They are also highly efficient as they can run continuously without the need for breaks or rest periods. However, automatic palletizing equipment is also the most expensive option and requires a significant initial investment. It may not be suitable for businesses with limited budgets or those with smaller production volumes.
Factors to consider when choosing palletizing equipment (production needs, space constraints, budget);
- When selecting palletizing equipment, understanding your production needs is crucial. Consider the volume of products you need to handle daily. Higher output may necessitate more advanced solutions.
- Space constraints play a significant role as well. Analyze your facility layout and determine how much room you can allocate for palletizing machinery. Compact designs might be essential in tighter spaces.
- The budget also cannot be overlooked. Assess both initial costs and long-term operational expenses. While automated systems offer efficiency, they often come with a higher price tag.
- Weighing these factors will help tailor the perfect solution for your operations, ensuring optimal productivity without compromising on safety or performance.
Benefits of using automated palletizing equipment;
Automated palletizing equipment offers a range of advantages that can transform your production line. Automated palletizing equipment has become a game-changer for industries that require efficient and speedy packing and shipping processes. It involves the use of advanced technology to stack products or goods on pallets, making them ready for transportation or storage. In this section, we will discuss the various benefits of using automated palletizing equipment.
1. Improved Efficiency and Productivity:
One of the most significant advantages of using automated palletizing equipment is its ability to improve efficiency and productivity in the packing and shipping process. The machines are designed to handle heavy loads quickly, accurately, and consistently without getting tired or requiring breaks. This helps reduce downtime and eliminates the need for manual labour, resulting in increased productivity.
2. Cost Savings:
Automated palletizing equipment offers long-term cost savings by reducing labour costs, minimizing product damage, and increasing operational efficiency. With manual palletizing methods, time-consuming tasks such as lifting heavy loads can lead to injuries and costly medical expenses for employees. Automated systems eliminate these risks while also reducing dependence on human labour.
3. Increased Safety:
Manual handling of heavy loads is not only physically demanding but also poses a risk of accidents or injuries in the workplace. By automating the palletizing process, workers are no longer required to lift heavy items manually, reducing the likelihood of injuries or musculoskeletal disorders caused by repetitive movements.
4. Consistency:
Another advantage of using automated palletizing equipment is consistency in stacking patterns and load configurations. The machines ensure that each layer is correctly aligned with minimal gaps between products for maximum stability during transportation or storage.
5. Flexibility:
Automated palletizers offer flexibility in terms of accommodating various package sizes and types without compromising speed or accuracy. With customizable options available for different packaging needs, businesses can quickly adapt their operations to meet changing market demands without major disruptions.
Automated palletizing equipment offers numerous benefits for businesses looking to streamline their packing and shipping processes. With increased efficiency, cost savings, improved safety, consistency, flexibility, and space optimization, it is no wonder that more industries are turning to this technology as a reliable solution for their palletizing needs.
Common features and technologies in modern palletizing systems;
Modern palletizing systems are equipped with an array of innovative features designed to enhance efficiency and reliability.
- One common technology is vision systems, which utilize cameras to identify products accurately. This ensures precise placement on pallets.
- Another notable feature is the integration of robotics. Robotic arms can handle a variety of product shapes and sizes, adapting quickly to changing demands. Their flexibility makes them invaluable in diverse production environments.
- Additionally, many systems now incorporate smart software for real-time monitoring and analytics. This allows operators to optimize performance by analyzing data related to throughput and downtime.
- Safety features such as emergency stop buttons and safety barriers are also standard in contemporary designs, protecting workers while ensuring seamless operations.
These advancements collectively contribute to streamlined workflows, reducing labor costs while increasing output quality significantly.
Maintenance and safety considerations for palletizing equipment;
Regular maintenance is key to ensuring the smooth operation of palletizing equipment. Schedule inspections to identify wear and tear before it leads to breakdowns. Lubricate moving parts frequently, as this can prevent unnecessary friction and prolong the lifespan of your machinery.
Safety should always be a top priority. Ensure that all safety guards are in place and functioning properly. Train your staff on safe operating procedures. Encourage them to report any irregularities immediately, reducing risks associated with malfunctioning equipment. Make use of technology for monitoring performance metrics. Many modern systems offer diagnostics that alert operators about potential issues before they escalate into serious problems.
Lastly, keep an organized work environment around the palletizing station. Clear pathways minimize accidents and ensure easy access during emergencies or maintenance tasks.
Conclusion:
Choosing the right palletizing equipment can significantly impact your operations. It’s essential to weigh all factors, including production needs, available space, and budget constraints.
Automated systems offer substantial benefits in terms of efficiency and consistency. However, manual and semi-automatic options still hold value for businesses with specific requirements or limited budgets. Understanding common features and technologies in modern systems is crucial for making an informed decision. Prioritize maintenance needs and safety protocols to ensure smooth operation.
Real-world examples highlight how tailored solutions lead to success stories across various industries. By assessing your unique situation carefully, you can find the perfect fit for your business’s palletizing needs.