Behind the Scenes: The Importance of Quality Control in Aircraft Parts Manufacturing
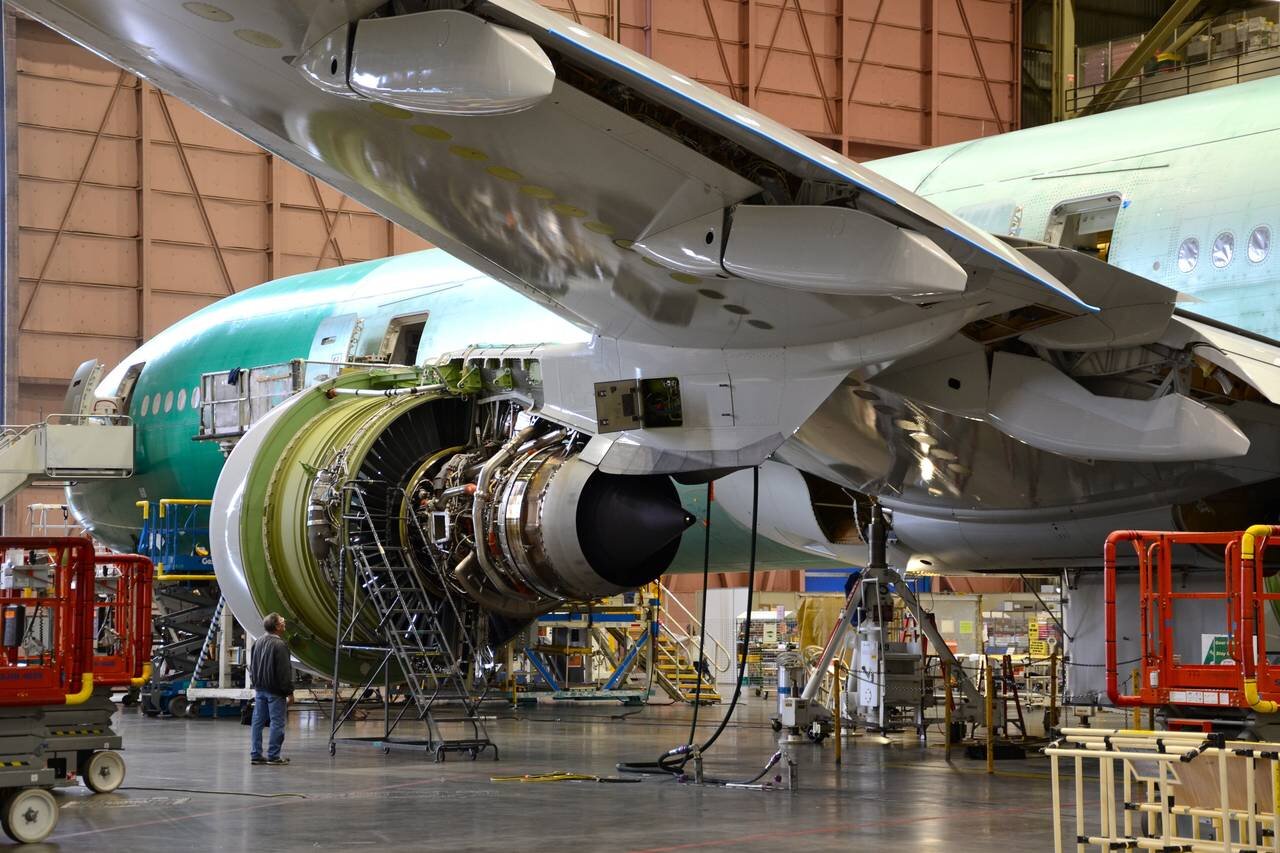
Introduction to the Aircraft Parts Manufacturing Industry;
The aircraft parts manufacturing industry is a complex and highly specialized field. Every component, no matter how small, plays a critical role in the safety and functionality of an aircraft. With millions of passengers flying every day, ensuring that these components meet rigorous standards is not just important—it’s essential.
In this high-stakes environment, quality control stands at the forefront. It’s more than just a set of procedures; it’s a commitment to excellence that can mean the difference between safe skies and catastrophic failures. As we delve deeper into this topic, you’ll discover why quality control isn’t merely an option—it’s a necessity in aerospace manufacturing. Join us as we explore what makes quality control so vital in creating reliable aircraft parts that keep our skies safe!
The Role of Quality Control in Aircraft Parts Manufacturing;
Quality control stands as a cornerstone in aircraft parts manufacturing. It ensures that every component meets rigorous standards before it takes to the skies.
From raw materials to final assembly, quality checkpoints are critical. Each phase involves meticulous inspections and tests aimed at identifying any defects early on. This proactive approach helps maintain high safety standards.Additionally, quality control fosters consistency across production lines. Uniformity is vital in aviation where even minor variations can lead to significant issues later.
Technological advancements also play a key role here. Automated systems and data analytics enhance precision during inspections, allowing for quick identification of anomalies.
The culture of continuous improvement thrives within organizations prioritizing quality control. Employees are trained not just to meet benchmarks but to elevate them consistently, driving innovation along the way.
Importance of Quality Control for Safety and Reliability;
Quality control is paramount in the aerospace industry. Every component of an aircraft plays a crucial role in its overall safety. A single faulty part can lead to catastrophic failures, endangering lives.Reliability stems from rigorous testing and validation processes throughout production. Each piece must meet stringent standards before it ever leaves the manufacturing floor. This meticulous attention to detail ensures that all parts function harmoniously when assembled.
Moreover, consistent quality assurance builds trust between manufacturers and airlines. Airlines depend on these components for safe operations. Any breach in quality can result not only in financial loss but also tarnish reputations built over decades.By investing time and resources into quality control measures, manufacturers uphold their commitment to safety and reliability, paving the way for innovation while prioritizing human life above all else.
Common Quality Control Processes in Aircraft Parts Manufacturing;
In aircraft parts manufacturing, quality control is a multi-faceted process. It begins with rigorous material inspection. Every batch of raw materials undergoes testing to ensure they meet stringent specifications.
Next comes in-process inspections during production. Skilled technicians monitor various stages, checking dimensions and tolerances against set standards. This real-time oversight helps catch defects early.Final product testing is equally crucial. Each component often faces extensive evaluation, including non-destructive testing methods like ultrasonic or X-ray examinations. These techniques reveal any hidden flaws without damaging the part.
Documentation plays a key role too. Detailed records track every step of inspection and testing processes, ensuring accountability and traceability throughout the supply chain.
Lastly, continuous monitoring through audits ensures that manufacturers adhere to established quality systems. Regular reviews keep everyone aligned with best practices in safety and efficiency within the aerospace industry.
Challenges and Solutions for Ensuring High-Quality Aircraft Parts;
Manufacturing aircraft parts involves numerous challenges that can affect quality. The manufacturing of aircraft parts is a complex process that requires precision, attention to detail, and strict adherence to safety standards. With thousands of parts that make up a single aircraft, ensuring the quality of each component is crucial for the overall safety and functionality of the aircraft. However, this task comes with its own set of challenges.
- One major challenge in ensuring high-quality aircraft parts is maintaining consistency in production. With such intricate designs and specifications, even the slightest deviation from the required measurements can result in faulty or subpar parts. This could potentially compromise the safety and performance of an aircraft. To address this challenge, manufacturers utilize advanced technologies like computer-aided design (CAD) software and computer numerical control (CNC) machines to ensure accuracy and consistency in production.
- Another key challenge is sourcing high-quality materials for manufacturing aircraft parts. The materials used must be durable enough to withstand extreme conditions such as high altitude, low temperatures, and intense pressure while also being lightweight to not add unnecessary weight to the aircraft. This requires stringent testing procedures and quality control measures to ensure only top-grade materials are used.
- Furthermore, another obstacle faced by manufacturers is adhering to strict regulatory requirements set by aviation authorities. Aviation safety regulations demand rigorous testing procedures and compliance with industry standards before any part can be deemed airworthy. This includes thorough inspections during different stages of production as well as final testing before installation on an aircraft.
- To overcome these challenges and ensure high-quality aircraft parts, manufacturers have implemented various solutions. One solution is implementing a robust quality control system throughout every stage of production. This involves conducting regular inspections at each step of the manufacturing process to identify any defects or deviations from specifications promptly.
- Additionally, investing in advanced inspection equipment such as x-ray machines or ultrasonic testing devices allows for more accurate detection of any flaws or weak points in a part’s structure that may not be visible to the naked eye. This helps to identify and rectify any potential issues before the parts are installed on an aircraft.
Ensuring high-quality aircraft parts is a challenging but essential aspect of the manufacturing process. By utilizing advanced technologies, implementing strict quality control measures, and adhering to regulatory requirements, manufacturers can overcome these challenges and produce top-grade components that meet the rigorous safety standards of the aviation industry.
The Impact of Quality Control on Cost and Efficiency;
Quality control significantly influences both cost and efficiency in aircraft parts manufacturing. By catching defects early, manufacturers can avoid the high costs associated with rework or scrapping faulty components. This proactive approach saves time and money.
Additionally, reliable quality control fosters streamlined operations. With standardized processes, manufacturers can produce parts more efficiently while maintaining consistency across batches. Reduced variability leads to fewer delays and smoother workflows.Moreover, strong quality assurance practices enhance supplier relationships. When parts meet stringent safety standards from the start, it minimizes disruptions down the line. Trust between partners grows as everyone benefits from a solid reputation for delivering reliable products.
Investing in advanced technology further boosts efficiency by automating inspections and tracking compliance data in real-time. This not only speeds up production but also ensures that resources are allocated effectively throughout the manufacturing process.
Future Developments in Quality Control for Aircraft Parts Manufacturing;
The future of quality control in aircraft parts manufacturing is poised for exciting innovations. Advanced technologies like artificial intelligence and machine learning are set to revolutionize how we monitor production processes. These tools can analyze vast amounts of data, identifying patterns that human inspectors might miss.
Automation will play a crucial role as well. With robots performing repetitive tasks, manufacturers can enhance precision while reducing the risk of human error. This shift allows engineers to focus on complex problem-solving and design improvements.Moreover, 3D printing technology is transforming prototyping and production methods. It enables rapid iteration, allowing teams to test and refine components quickly before full-scale manufacturing begins.
Collaboration with industry stakeholders will also grow stronger, streamlining communication between suppliers, manufacturers, and regulatory bodies. As these developments unfold, they promise to create safer skies through improved quality assurance practices in the aerospace sector.
Conclusion:
Quality control stands as a pillar in the aircraft parts manufacturing sector. It directly affects safety, reliability, and performance in aviation. Each component must meet stringent standards to ensure that every flight is safe and efficient.
The consequences of neglecting quality can be dire. A single faulty part can lead to catastrophic failures. Therefore, manufacturers invest heavily in rigorous testing and inspection protocols throughout their processes.Furthermore, effective quality control fosters trust among stakeholders—from manufacturers to airlines and passengers alike. It’s not only about compliance; it’s about building a reputation for excellence.
As technology evolves, so do the methods of ensuring quality. Innovations like AI-driven inspections and advanced materials are shaping the future landscape of aerospace manufacturing.Ultimately, prioritizing quality control enhances both operational efficiency and cost-effectiveness for companies while safeguarding lives in the skies. Without it, the industry simply cannot thrive or maintain its high standards.