Die Casting Service: Precision Manufacturing for Complex Parts
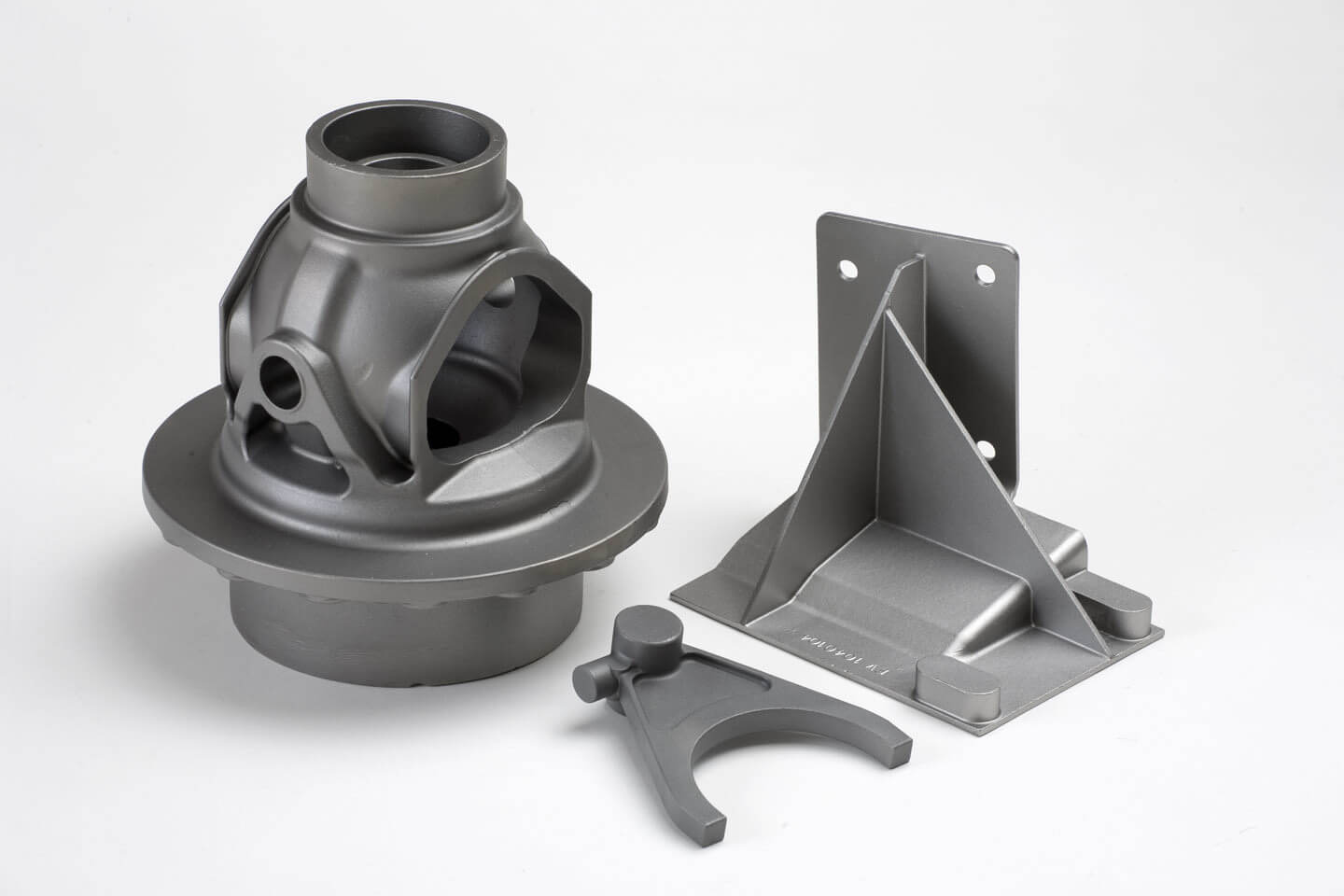
Die casting is a highly efficient manufacturing process used to produce intricate and complex parts with excellent dimensional accuracy and surface finish. In this article, we will explore the key aspects, benefits, applications, and considerations associated with die casting services.
Understanding Die Casting:
Die casting is a metal casting process that involves forcing molten metal into a mold cavity under high pressure. The mold, called a die, is typically made of steel and consists of two halves that form the desired shape of the part. Once the metal solidifies, the die is opened, and the casting is ejected, resulting in a precise and detailed component.
Advantages of Die Casting Services:
1. High Precision: Die casting offers tight tolerances and excellent dimensional accuracy, making it suitable for parts with intricate geometries and complex features.
2. Complex Shapes: Die casting can produce parts with thin walls, sharp corners, and intricate details that are difficult to achieve with other die casting service manufacturing processes.
3. Consistency: The die casting process ensures consistent part quality and reproducibility, reducing variations and maintaining uniformity across production runs.
4. Cost-Effectiveness: Die casting is a cost-effective method for mass production of parts due to high production rates, minimal material waste, and reduced machining requirements.
5. Versatility: Die casting services can work with a wide range of metals and alloys, including aluminum, zinc, magnesium, and brass, offering versatility in material selection.
Applications of Die Casting Services:
1. Automotive Industry: Die casting produces engine components, transmission parts, chassis components, and decorative trim for automobiles and motorcycles.
2. Consumer Electronics: Die casting creates housings, frames, heat sinks, and structural components for smartphones, laptops, cameras, and other electronic devices.
3. Industrial Equipment: Die casting manufactures parts for machinery, pumps, valves, hydraulic components, and industrial tools requiring high strength and precision.
4. Appliances: Die casting produces components for appliances such as refrigerators, washing machines, air conditioners, and cooking equipment.
5. Lighting and Fixtures: Die casting services fabricate components for lighting fixtures, lamp housings, brackets, and architectural hardware.
Considerations for Choosing Die Casting Services:
1. Material Selection: Choose a die casting service provider that offers a range of materials suitable for your application, considering factors such as mechanical properties, corrosion resistance, and cost.
2. Tooling and Equipment: Evaluate the die casting company’s capabilities in terms of die design, tooling development, and equipment capacity to meet your production requirements.
3. Quality Assurance: Ensure that the die casting service provider follows strict quality control measures, conducts inspections, and provides certifications to guarantee part quality and compliance.
4. Experience and Expertise: Select a die casting partner with experience, technical expertise, and a proven track record in producing high-quality die castings for your industry or application.
5. Cost and Lead Times: Consider the cost-effectiveness and lead times offered by different die casting services, balancing quality, pricing, and production schedules for optimal results.
Conclusion:
Die casting services offer precision, efficiency, and versatility in manufacturing complex parts for various industries. By understanding the advantages, applications, considerations, and key factors to consider when choosing a die casting service provider, businesses can leverage this advanced manufacturing process to produce high-quality components that meet their specific requirements and standards.