Powering the Future: Electric Vehicle Engineering Plastics – An Evolutionary Marvel
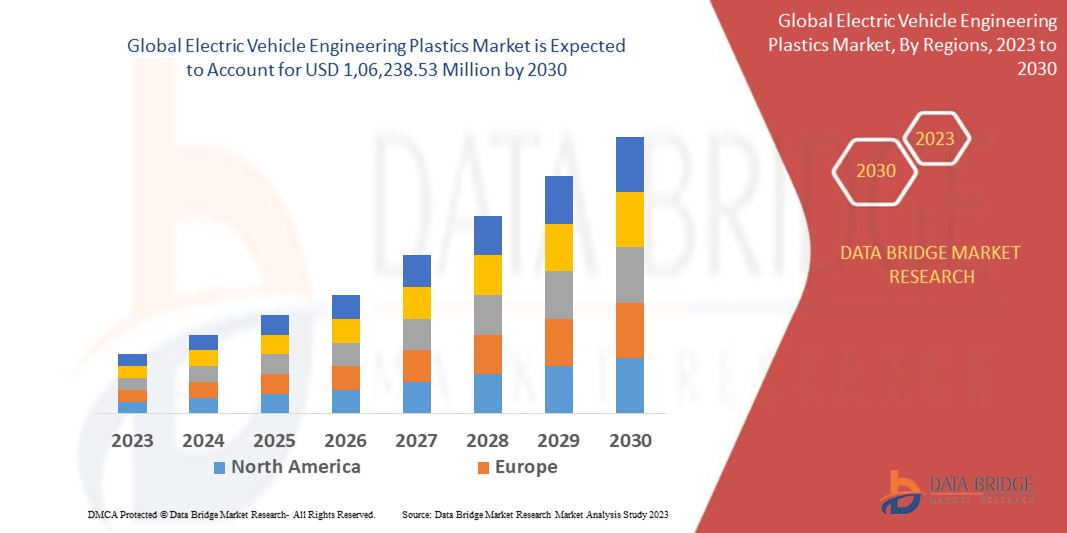
Introduction
The automotive industry is undergoing a revolutionary shift, and at the heart of this transformation lies the realm of Electric Vehicle (EV) Engineering Plastics. As the world embraces sustainable mobility solutions, the demand for electric vehicles has skyrocketed, bringing to the forefront the crucial role of specialized engineering plastics. This guest post delves into the introduction, evolution, current market trends, and the factors propelling the extraordinary growth of Electric Vehicle Engineering Plastics.
The Evolution
The evolution of Electric Vehicle Engineering Plastics mirrors the rapid advancements and innovations within the electric vehicle sector. Historically, the automotive industry predominantly relied on traditional materials like steel and aluminum. However, the unique challenges and requirements posed by electric vehicles paved the way for the development and integration of engineering plastics.
The quest for lightweight materials that offer high strength, durability, and thermal resistance led to the emergence of engineering plastics such as polycarbonates, polyamides, and polyesters in the electric vehicle landscape. These materials, known for their versatility and adaptability, have become instrumental in addressing key engineering challenges associated with electric vehicles.
One of the primary drivers for the adoption of engineering plastics in electric vehicles is their weight reduction capability. Unlike conventional vehicles, electric vehicles rely heavily on battery technology, and minimizing overall vehicle weight is crucial for optimizing energy efficiency and extending driving range. Engineering plastics, with their high strength-to-weight ratio, provide an ideal solution to meet these requirements.
Furthermore, the evolution of Electric Vehicle Engineering Plastics is deeply entwined with the pursuit of enhanced aerodynamics, thermal management, and design flexibility. Plastics allow for intricate designs, streamlined shapes, and improved airflow, contributing not only to the efficiency of electric vehicles but also to their aesthetic appeal.
Market Trends
The market for Electric Vehicle Engineering Plastics is dynamic, shaped by technological advancements, regulatory changes, and the growing prominence of electric vehicles in the automotive landscape. Several key trends have emerged, influencing the adoption and application of engineering plastics in electric vehicles.
- Battery Encapsulation: With electric vehicles relying heavily on advanced battery technologies, the demand for materials that ensure the safety and efficiency of battery enclosures is on the rise. Engineering plastics play a pivotal role in battery encapsulation, providing insulation, thermal management, and mechanical strength to protect the sensitive battery components.
- Interior Components: The interior of electric vehicles is witnessing a transformation, and engineering plastics are at the forefront of this change. Lightweight and durable plastics are used in the manufacturing of interior components such as panels, trims, and dashboard elements. This not only contributes to weight reduction but also enhances the overall aesthetics and design flexibility of electric vehicle interiors.
- Exterior Components: The exterior design of electric vehicles places a premium on aerodynamics and energy efficiency. Engineering plastics, with their malleability and resistance to environmental factors, are increasingly utilized in the production of exterior components. From body panels to specialized aerodynamic features, plastics contribute to the overall efficiency and performance of electric vehicles.
- Charging Infrastructure: As the electric vehicle charging infrastructure expands globally, the need for robust and weather-resistant components becomes paramount. Engineering plastics, known for their durability and resistance to harsh environmental conditions, are employed in the manufacturing of charging station components. This trend is set to grow as the charging network continues to evolve.
Factors Driving Growth
The growth of Electric Vehicle Engineering Plastics is propelled by a confluence of factors that address the unique challenges and opportunities presented by electric vehicles.
- Lightweighting and Efficiency: The paramount need for lightweight materials to enhance energy efficiency and extend driving range is a major driver for the adoption of engineering plastics. By replacing traditional materials with lightweight plastics, electric vehicles can achieve a favorable balance between weight reduction and structural integrity.
- Design Flexibility: Electric vehicles offer a canvas for innovative design, and engineering plastics provide the necessary flexibility to turn design concepts into reality. The ability to mold and shape plastics into intricate designs allows automakers to create aerodynamic and aesthetically pleasing electric vehicles, setting them apart from their conventional counterparts.
- Sustainability and Recycling: The automotive industry, in line with global sustainability goals, is increasingly focused on environmentally friendly materials and manufacturing processes. Engineering plastics, when sourced responsibly and designed for recyclability, contribute to the overall sustainability of electric vehicles. The development of recyclable plastics is gaining traction as manufacturers aim to reduce the environmental impact of electric vehicle production.
- Regulatory Mandates: Governments worldwide are introducing stringent emissions regulations and promoting the adoption of electric vehicles to combat climate change. In response, automakers are accelerating the transition to electric vehicles, driving the demand for engineering plastics that align with regulatory requirements. These plastics not only enhance vehicle performance but also contribute to meeting emissions targets.
Conclusion
In conclusion, Electric Vehicle Engineering Plastics have emerged as a driving force in the transformative journey of the automotive industry towards sustainability and efficiency. From addressing the unique challenges of electric vehicles to influencing their design and performance, engineering plastics have become indispensable in the electric mobility landscape.
As the market continues to evolve, the demand for innovative engineering plastics will likely surge, driven by the ongoing electrification of vehicles and the push for sustainable transportation solutions. The evolution of Electric Vehicle Engineering Plastics is a testament to the resilience and adaptability of the automotive industry as it strives to power the future with clean, efficient, and technologically advanced electric vehicles.